In the world of manufacturing, efficient planning is the backbone of seamless operations—and Material Requirements Planning (MRP) plays a central role in making that possible. But what powers the MRP engine to generate accurate material plans? It all starts with a well-structured Bill of Materials (BOM).
This blog explores what MRP is and how a well-structured BOM supports and strengthens the requirements planning process within MRP systems. You’ll learn how MRP uses BOM data to calculate material needs, what sources of demand drive those calculations, the challenges MRP helps solve, and how it translates into real-world operational impact across departments like procurement, production, inventory, and finance.
What is Material Requirements Planning (MRP)?
Material Requirements Planning (MRP) is a method used to manage manufacturing processes by ensuring that materials are available when needed, reducing excess inventory, and optimizing production scheduling. It aligns material demand with available inventory, scheduled receipts, and proposes requirements for raising purchase orders and work orders. By synchronizing material availability with production priorities and capacity, the MRP process minimizes shortages and lateness, prevents overstocking, and promotes efficient use of resources throughout the manufacturing workflow.
What are the Key Elements MRP Depends on?- Master Production Schedule (MPS):
Defines what products need to be produced, in what quantity, and by when. It acts as the primary input driving all material planning decisions in MRP. - Bill of Materials (BOM):
Provides the complete breakdown of all components and sub-assemblies needed to build each product. MRP uses this to determine the quantity of material requirements. - Inventory Data:
Reflects the current stock levels and availability of materials. Accurate inventory data helps MRP calculate what needs to be procured or produced, avoiding overstocking or stockouts. - External Demand Signals:
Defines dynamic inputs such as customer sales orders, stock transfers, and forecasts, which are utilized in the MRP process to compute material requirements.
These inputs - internal requirements like MPS and inventory data, and external requirements like customer sales orders and forecasts, work together as key inputs for the MRP process. Meanwhile, the BOM acts as the recipe for production, helping the MRP engine answer key planning questions: (i) What do we need? (ii) How much do we need? and (iii) When do we need it?
Importance of BOM in MRP
The Bill of Materials (BOM) plays a foundational role in the Material Requirements Planning (MRP) process, serving as a core input that outlines all components, assemblies, and sub-assemblies needed to manufacture a finished product. This detailed breakdown is essential for accurately matching material demand with supply.
Without a well-structured BOM, the MRP engine cannot generate reliable procurement or production plans, leading to potential inefficiencies and disruptions. Whether maintained in a sophisticated MRP system or a simple spreadsheet, an accurate BOM feeds critical data into the planning engine. It aids in minimizing errors while avoiding stock imbalances, and ensures smoother production flows.
In the broader context, a clear and updated BOM supports better resource utilization, reduces costs, improves cross-functional coordination, and enables confident, data-driven decision-making, making it a vital component of efficient and scalable manufacturing operations.
Real-World Scenario: How BOM Drives MRP in Skateboard Manufacturing
To illustrate the role of BOM in MRP, let’s walk through a simplified manufacturing scenario for a skateboard.
Product: Skateboard
BOM Breakdown:
Each skateboard requires:
- 2 Stickers,
- 1 Warranty Card,
- 1 Transfer,
- 1 Deck.
The Deck itself is internally manufactured using 1 unit of each:
- Glue (1 unit = 1 single-use glue capsule),
- Ply,
- Face,
- Core
A minimum stock level of 20 units is set for all components.
Sales Demand:
ABC Company receives sales orders totaling 500 skateboards.
Now, the MRP engine uses this BOM to calculate exactly how much of each material is needed:
- Stickers: 2 per skateboard
⇒ (500 × 2) + 20 minimum stock = 1020 units required
If current stock is 100, MRP suggests 920 units to procure. - Warranty Cards & Transfers: 1 per skateboard
⇒ (500 × 1) + 20 minimum stock = 520 units required
If current stock is 100, MRP suggests 420 units to procure. - Sub-Components for Deck (Glue, Ply, Face, Core): 1 per skateboard
⇒ (500 × 1) + 20 minimum stock = 520 units required
If current stock is 100, MRP suggests 420 units to procure for each of the sub-components.
The Skateboard and Deck are produced in-house, so MRP doesn’t propose procurement but still calculates that 520 units need to be produced to meet both sales orders and minimum stock requirements.
[Note: if the sub-assembly (i.e., the Deck) already has 100 units in stock and a minimum stock requirement of 20 units, then only 420 additional Deck units would need to be produced]
Summary of Material Requirements generated:
- Stickers: 920 units
- Warranty Cards: 420 units
- Transfers: 420 units
- Glue, Ply, Face, Core (Deck parts): 420 units each
- Deck: 520 units (internally produced)
- Skateboard: 520 units (internally produced)
Through this skateboard manufacturing example, we’ve shown how the BOM is an essential input driving the MRP calculation. By breaking down the skateboard into its components and sub-assemblies, the BOM provides the MRP engine with the data needed to calculate exactly how much of each material is required—right down to the glue and ply used in the deck. Without this detailed structure, MRP wouldn't be able to translate the 500 skateboard sales orders into precise material requirements.
Conclusion
As demonstrated, MRP helps accurately calculate the material requirements to fulfill both internal and external demands, ensuring that supply matches demand. It ensures that materials are procured, produced, stocked, and used efficiently, preventing costly disruptions. This process is only possible when a well-structured and accurate BOM acts as the foundation, giving the MRP engine the necessary details to determine the exact quantities of raw materials required for production. By investing in BOM accuracy, businesses can achieve higher operational efficiency, cost savings, and improved production planning. Choosing the right MRP software is also a critical step that could streamline the MRP process and further optimize operations.
If your business is looking for a smart MRP solution, HotWax Systems can help you set up and customize Apache OFBiz to streamline your material requirements planning. By leveraging HotWax Accelerator, you can enhance your Apache OFBiz implementation with accelerated development, seamless integrations, and powerful real-time insights to gain operational efficiency and faster growth across your supply chain.
Connect with HotWax Systems today to explore how Apache OFBiz and HotWax Accelerator can transform your manufacturing processes!
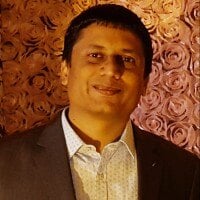